Silisyum karbür dirençli uzun kristal fırın 6/8/12 inç inç SiC külçe kristal PVT yöntemi yetiştiriyor
Çalışma prensibi:
1. Hammadde yükleme: Grafit potanın tabanına (yüksek sıcaklık bölgesi) yerleştirilen yüksek saflıktaki SiC tozu (veya bloğu).
2. Vakum/inert ortam: Fırın bölmesini vakumlayın (<10⁻³ mbar) veya inert gaz (Ar) geçirin.
3. Yüksek sıcaklıkta süblimleşme: 2000~2500℃'ye kadar direnç ısıtma, SiC'nin Si, Si₂C, SiC₂ ve diğer gaz fazı bileşenlerine ayrışması.
4. Gaz fazı iletimi: Sıcaklık gradyanı, gaz fazı malzemesinin düşük sıcaklık bölgesine (tohum ucu) difüzyonunu sağlar.
5. Kristal büyümesi: Gaz fazı Tohum Kristalin yüzeyinde yeniden kristalleşir ve C ekseni veya A ekseni boyunca yönlü bir yönde büyür.
Anahtar parametreler:
1. Sıcaklık gradyanı: 20~50℃/cm (büyüme hızını ve kusur yoğunluğunu kontrol edin).
2. Basınç: 1~100mbar (kirlilik katılımını azaltmak için düşük basınç).
3.Büyüme hızı: 0,1~1mm/h (kristal kalitesini ve üretim verimliliğini etkiler).
Başlıca özellikleri:
(1) Kristal kalitesi
Düşük kusur yoğunluğu: mikrotübül yoğunluğu <1 cm⁻², çıkık yoğunluğu 10³~10⁴ cm⁻² (tohum optimizasyonu ve proses kontrolü yoluyla).
Polikristalin tip kontrolü: 4H-SiC (ana akım), 6H-SiC, 4H-SiC oranı >%90'ı büyütebilir (sıcaklık gradyanını ve gaz fazı stokiyometrik oranını doğru bir şekilde kontrol etmek gerekir).
(2) Ekipman performansı
Yüksek sıcaklık kararlılığı: grafit ısıtma gövdesi sıcaklığı >2500℃, fırın gövdesi çok katmanlı yalıtım tasarımını benimser (grafit keçe + su soğutmalı ceket gibi).
Tekdüzelik kontrolü: ±5 °C'lik eksenel/radyal sıcaklık dalgalanmaları kristal çapının tutarlılığını sağlar (6 inçlik alt tabaka kalınlığı sapması <%5).
Otomasyon derecesi: Entegre PLC kontrol sistemi, sıcaklık, basınç ve büyüme hızının gerçek zamanlı izlenmesi.
(3) Teknolojik avantajlar
Yüksek malzeme kullanımı: Hammadde dönüşüm oranı >%70 (CVD yönteminden daha iyi).
Büyük boyut uyumluluğu: 6 inç seri üretime ulaşıldı, 8 inç ise geliştirilme aşamasında.
(4) Enerji tüketimi ve maliyeti
Tek bir fırının enerji tüketimi 300~800kW·h olup, SiC alt tabaka üretim maliyetinin %40~60'ını oluşturmaktadır.
Ekipman yatırımı yüksektir (birim başına 1,5M-3M), ancak birim alt tabaka maliyeti CVD yöntemine göre daha düşüktür.
Temel uygulamalar:
1. Güç elektroniği: Elektrikli araç invertörü ve fotovoltaik invertör için SiC MOSFET alt tabakası.
2. Rf cihazları: 5G baz istasyonu GaN-on-SiC epitaksiyel alt tabaka (çoğunlukla 4H-SiC).
3. Aşırı ortam cihazları: Havacılık ve nükleer enerji ekipmanları için yüksek sıcaklık ve yüksek basınç sensörleri.
Teknik parametreler:
Şartname | Detaylar |
Boyutlar (U × G × Y) | 2500 × 2400 × 3456 mm veya özelleştirin |
Pota Çapı | 900 mm |
Son Vakum Basıncı | 6 × 10⁻⁴ Pa (1,5 saatlik vakumdan sonra) |
Sızıntı Oranı | ≤5 Pa/12h (pişirme) |
Dönme Şaft Çapı | 50 mm |
Dönme Hızı | 0,5–5 dev/dak |
Isıtma Yöntemi | Elektrikli direnç ısıtması |
Maksimum Fırın Sıcaklığı | 2500°C |
Isıtma Gücü | 40kW × 2×20kW |
Sıcaklık Ölçümü | Çift renkli kızılötesi pirometre |
Sıcaklık Aralığı | 900–3000°C |
Sıcaklık Doğruluğu | ±1°C |
Basınç Aralığı | 1–700 mbar |
Basınç Kontrol Doğruluğu | 1–10 mbar: ±%0,5 FS; 10–100 mbar: ±%0,5 FS; 100–700 mbar: ±%0,5 FS |
İşlem Türü | Alt yükleme, manuel/otomatik güvenlik seçenekleri |
İsteğe bağlı özellikler | Çift sıcaklık ölçümü, çoklu ısıtma bölgeleri |
XKH Hizmetleri:
XKH, müşterilerin yüksek kaliteli sic kristal seri üretimine ulaşmalarına yardımcı olmak için ekipman özelleştirme (termal alan tasarımı, otomatik kontrol), proses geliştirme (kristal şekil kontrolü, kusur optimizasyonu), teknik eğitim (işletme ve bakım) ve satış sonrası destek (grafit parça değişimi, termal alan kalibrasyonu) dahil olmak üzere SiC PVT fırınının tüm proses hizmetini sağlar. Ayrıca, tipik olarak 3-6 aylık bir teslim süresiyle kristal verimini ve büyüme verimliliğini sürekli olarak iyileştirmek için proses yükseltme hizmetleri de sağlıyoruz.
Ayrıntılı Diyagram
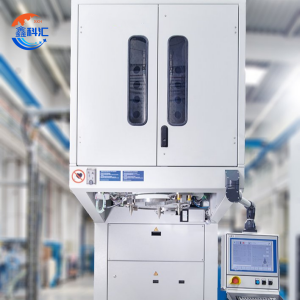
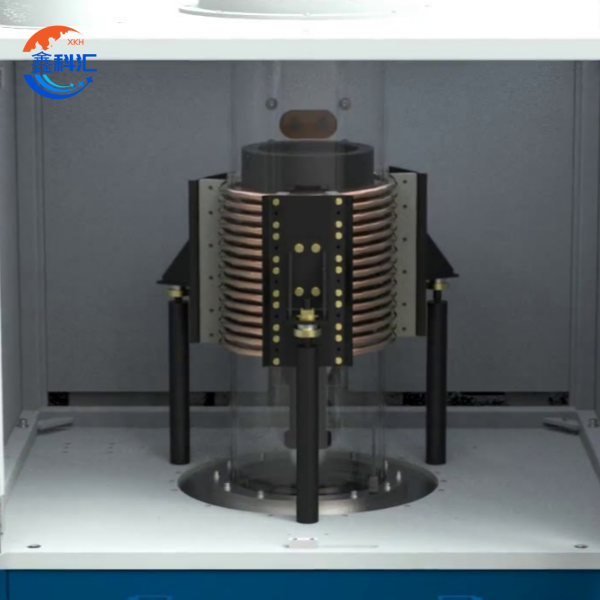
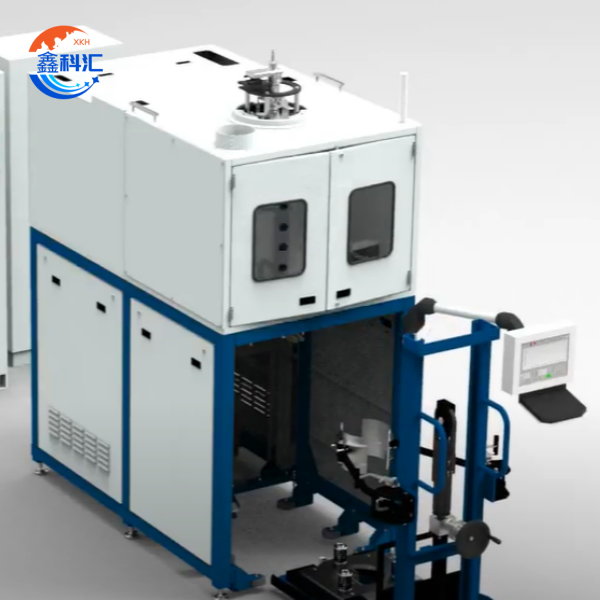