Yarı iletken üretim sürecinde kritik bir adım olan yonga kesme teknolojisi, çip performansı, verimi ve üretim maliyetleriyle doğrudan bağlantılıdır.
#01 Wafer Dicing'in Arka Planı ve Önemi
1.1 Wafer Dicing'in Tanımı
Wafer kesme (ayrıca yazma olarak da bilinir) yarı iletken üretiminde işlenmiş wafer'ları birden fazla ayrı kalıba bölmeyi amaçlayan temel bir adımdır. Bu kalıplar genellikle tam devre işlevselliği içerir ve elektronik cihazların üretiminde nihai olarak kullanılan temel bileşenlerdir. Çip tasarımları daha karmaşık hale geldikçe ve boyutlar küçülmeye devam ettikçe, wafer kesme teknolojisi için hassasiyet ve verimlilik gereksinimleri giderek daha katı hale geliyor.
Pratik operasyonlarda, wafer kesme işlemi genellikle her kalıbın sağlam ve tam işlevsel kalmasını sağlamak için elmas bıçaklar gibi yüksek hassasiyetli aletler kullanır. Temel adımlar arasında kesmeden önce hazırlık, kesme işlemi sırasında hassas kontrol ve kesmeden sonra kalite denetimi yer alır.
Kesmeden önce, doğru kesme yollarının sağlanması için gofret işaretlenmeli ve konumlandırılmalıdır. Kesme sırasında, gofrete zarar gelmesini önlemek için takım basıncı ve hızı gibi parametreler sıkı bir şekilde kontrol edilmelidir. Kesmeden sonra, her çipin performans standartlarını karşıladığından emin olmak için kapsamlı kalite denetimleri yapılır.
Wafer kesme teknolojisinin temel prensipleri yalnızca kesme ekipmanının seçimini ve işlem parametrelerinin ayarlanmasını değil aynı zamanda malzemelerin mekanik özelliklerinin ve karakteristiklerinin kesme kalitesi üzerindeki etkisini de kapsar. Örneğin, düşük-k dielektrik silikon wafer'lar, düşük mekanik özellikleri nedeniyle, kesme sırasında gerilim yoğunlaşmasına karşı oldukça hassastır ve bu da kırılma ve çatlama gibi arızalara yol açar. Düşük-k malzemelerin düşük sertliği ve kırılganlığı, özellikle kesme sırasında mekanik kuvvet veya termal gerilim altında yapısal hasara daha yatkın hale getirir. Alet ile wafer yüzeyi arasındaki temas, yüksek sıcaklıklarla birleştiğinde gerilim yoğunlaşmasını daha da kötüleştirebilir.
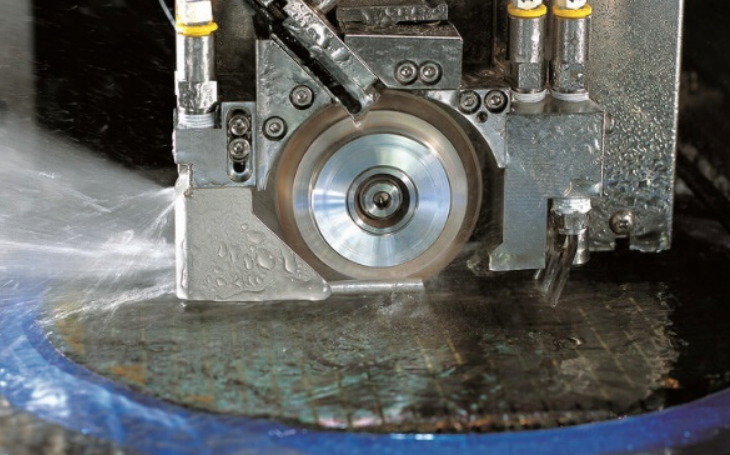
Malzeme bilimindeki gelişmelerle birlikte, yonga kesme teknolojisi geleneksel silikon tabanlı yarı iletkenlerin ötesine geçerek galyum nitrür (GaN) gibi yeni malzemeleri de kapsayacak şekilde genişledi. Bu yeni malzemeler, sertlikleri ve yapısal özellikleri nedeniyle kesme işlemleri için yeni zorluklar ortaya koyuyor ve kesme aletleri ve tekniklerinde daha fazla iyileştirme gerektiriyor.
Yarı iletken endüstrisinde kritik bir işlem olan yonga kesme işlemi, değişen taleplere ve teknolojik gelişmelere yanıt olarak optimize edilmeye devam ediyor ve gelecekteki mikroelektronik ve entegre devre teknolojilerinin temelini oluşturuyor.
Wafer kesme teknolojisindeki gelişmeler yardımcı malzemelerin ve araçların geliştirilmesinin ötesine geçer. Ayrıca süreç optimizasyonunu, ekipman performansındaki iyileştirmeleri ve kesme parametrelerinin hassas kontrolünü de kapsar. Bu gelişmeler, yarı iletken endüstrisinin daha küçük boyutlara, daha yüksek entegrasyona ve daha karmaşık çip yapılarına olan ihtiyacını karşılayarak wafer kesme sürecinde yüksek hassasiyet, verimlilik ve kararlılık sağlamayı amaçlamaktadır.
İyileştirme Alanı | Belirli Önlemler | Etkileri |
Süreç Optimizasyonu | - Daha hassas gofret konumlandırma ve yol planlama gibi ilk hazırlıkları iyileştirin. | - Kesim hatalarını azaltın ve stabiliteyi artırın. |
- Kesim hatalarını en aza indirin ve stabiliteyi artırın. | - Takım basıncını, hızını ve sıcaklığını ayarlamak için gerçek zamanlı izleme ve geri bildirim mekanizmalarını benimseyin. | |
- Wafer kırılma oranlarını düşürün ve çip kalitesini artırın. | ||
Ekipman Performansının Geliştirilmesi | - Yüksek hassasiyetli mekanik sistemler ve ileri otomasyon kontrol teknolojisinden faydalanmak. | - Kesim hassasiyetini artırın ve malzeme israfını azaltın. |
- Yüksek sertlikteki malzeme gofretlerine uygun lazer kesim teknolojisini tanıtmak. | - Üretim verimliliğini artırın ve manuel hataları azaltın. | |
- Otomatik izleme ve ayarlamalar için ekipman otomasyonunu artırın. | ||
Hassas Parametre Kontrolü | - Kesme derinliği, hız, takım tipi ve soğutma yöntemleri gibi parametreleri hassas bir şekilde ayarlayın. | - Kalıp bütünlüğünü ve elektriksel performansı garantileyin. |
- Wafer malzemesine, kalınlığına ve yapısına göre parametreleri özelleştirin. | - Verim oranlarını artırın, malzeme israfını azaltın ve üretim maliyetlerini düşürün. | |
Stratejik Önem | - Pazar taleplerini karşılamak için sürekli olarak yeni teknolojik yollar keşfetmek, süreçleri optimize etmek ve ekipman kapasitelerini geliştirmek. | - Yeni malzemelerin ve gelişmiş çip tasarımlarının geliştirilmesini destekleyerek çip üretim verimini ve performansını artırmak. |
1.2 Wafer Dicing'in Önemi
Wafer kesme, yarı iletken üretim sürecinde kritik bir rol oynar ve sonraki adımların yanı sıra nihai ürünün kalitesini ve performansını doğrudan etkiler. Önemi aşağıdaki gibi ayrıntılı olarak açıklanabilir:
Öncelikle, kesme işleminin doğruluğu ve tutarlılığı, çip verimini ve güvenilirliğini sağlamanın anahtarıdır. Üretim sırasında, wafer'lar çok sayıda karmaşık devre yapısı oluşturmak için birden fazla işleme adımından geçer ve bu yapılar hassas bir şekilde ayrı çiplere (kalıplara) bölünmelidir. Kesme işlemi sırasında hizalama veya kesmede önemli hatalar varsa, devreler hasar görebilir ve çipin işlevselliği ve güvenilirliği etkilenebilir. Bu nedenle, yüksek hassasiyetli kesme teknolojisi yalnızca her çipin bütünlüğünü sağlamakla kalmaz, aynı zamanda dahili devrelere zarar gelmesini önleyerek genel verim oranını iyileştirir.
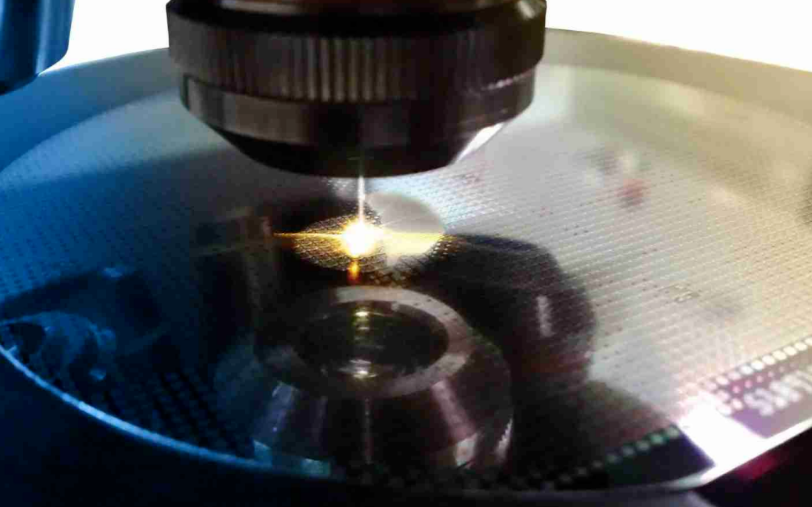
İkinci olarak, wafer kesme işleminin üretim verimliliği ve maliyet kontrolü üzerinde önemli bir etkisi vardır. Üretim sürecinde kritik bir adım olarak verimliliği, sonraki adımların ilerlemesini doğrudan etkiler. Kesme işlemini optimize ederek, otomasyon seviyelerini artırarak ve kesme hızlarını iyileştirerek genel üretim verimliliği büyük ölçüde artırılabilir.
Öte yandan, kesme sırasında malzeme israfı maliyet yönetiminde kritik bir faktördür. Gelişmiş kesme teknolojilerinin kullanılması, kesme işlemi sırasında gereksiz malzeme kayıplarını azaltmakla kalmaz, aynı zamanda gofret kullanımını da artırarak üretim maliyetlerini düşürür.
Yarı iletken teknolojisindeki gelişmelerle birlikte, yonga çapları artmaya devam ediyor ve devre yoğunlukları da buna bağlı olarak yükseliyor ve bu da kesme teknolojisine yönelik talepleri artırıyor. Daha büyük yongalar, özellikle küçük sapmaların bile birden fazla çipi arızalı hale getirebileceği yüksek yoğunluklu devre alanlarında, kesme yollarının daha hassas bir şekilde kontrol edilmesini gerektirir. Ek olarak, daha büyük yongalar daha fazla kesme çizgisi ve daha karmaşık işlem adımları içerir ve bu da bu zorlukların üstesinden gelmek için kesme teknolojilerinin hassasiyetinde, tutarlılığında ve verimliliğinde daha fazla iyileştirme gerektirir.
1.3 Wafer Kesme İşlemi
Wafer kesme işlemi, hazırlama aşamasından son kalite denetimine kadar tüm adımları kapsar ve her aşama, kesilmiş yongaların kalitesini ve performansını garantilemek için kritik öneme sahiptir. Aşağıda her aşamanın ayrıntılı açıklaması bulunmaktadır.
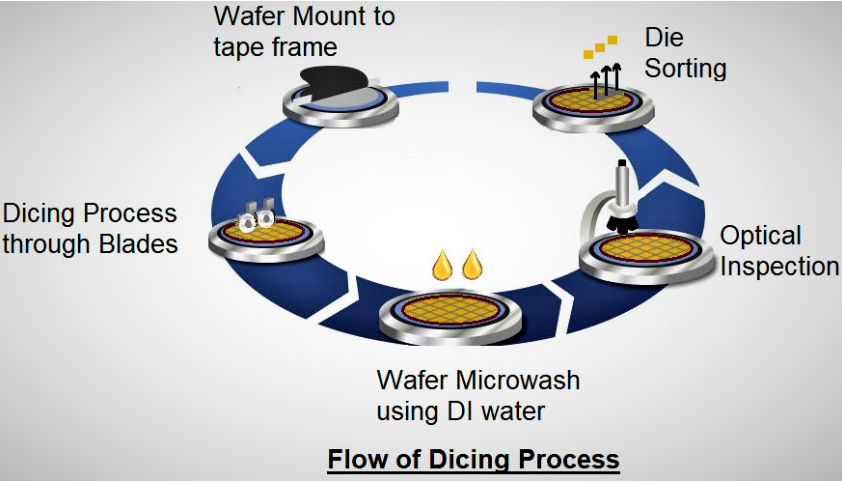
Faz | Ayrıntılı Açıklama |
Hazırlık Aşaması | -Wafer Temizleme: Yüksek saflıkta su ve özel temizlik maddeleri ile ultrasonik veya mekanik fırçalamanın birleşimini kullanarak kirleri, parçacıkları ve kirleticileri temizleyerek temiz bir yüzey elde edin. -Hassas Konumlandırma:Tasarlanan kesme yolları boyunca yonganın doğru bir şekilde bölünmesini sağlamak için yüksek hassasiyetli ekipman kullanın. -Wafer Sabitleme: Kesim sırasında stabiliteyi korumak ve titreşim veya hareketten kaynaklanabilecek hasarı önlemek için gofreti bir bant çerçevesine sabitleyin. |
Kesme Aşaması | -Bıçakla Kesme:Fiziksel kesme için yüksek hızlı dönen elmas kaplı bıçaklar kullanın, silikon esaslı malzemeler için uygun ve maliyet açısından verimlidir. -Lazerle kesme:Galyum nitrür gibi kırılgan veya yüksek sertlikteki malzemeler için ideal olan, temas gerektirmeyen kesim için yüksek enerjili lazer ışınlarından yararlanın, daha yüksek hassasiyet ve daha az malzeme kaybı sağlayın. -Yeni Teknolojiler: Verimliliği ve hassasiyeti daha da artırmak, ısıdan etkilenen bölgeleri en aza indirmek için lazer ve plazma kesim teknolojilerini tanıtın. |
Temizlik Aşaması | - Kesme işlemi sırasında oluşan kalıntıları ve tozu temizlemek için ultrasonik veya sprey temizleme ile birlikte deiyonize su (DI su) ve özel temizlik maddeleri kullanın, böylece kalıntıların sonraki işlemleri veya çipin elektriksel performansını etkilemesini önleyin. - Yüksek saflıktaki DI suyu, yeni kirleticilerin girmesini önleyerek temiz bir gofret ortamı sağlar. |
Muayene Aşaması | -Optik Muayene: Kusurları hızlı bir şekilde tespit etmek, küp küp doğranmış parçalarda çatlak veya kırılma olmadığından emin olmak, denetim verimliliğini artırmak ve insan hatasını azaltmak için yapay zeka algoritmalarıyla birleştirilmiş optik algılama sistemlerini kullanın. -Boyut Ölçümü:Çip boyutlarının tasarım özelliklerine uygun olduğunu doğrulayın. -Elektriksel Performans Testi:Kritik yongaların elektriksel performansının standartlara uygun olmasını sağlayarak, sonraki uygulamalarda güvenilirliği garanti altına alın. |
Sıralama Aşaması | - Nitelikli talaşları bant çerçevesinden ayırmak ve bunları performansa göre otomatik olarak sıralamak için robotik kollar veya vakumlu vantuzları kullanın, böylece hassasiyeti artırırken üretim verimliliği ve esnekliğini garantileyin. |
Wafer kesme işlemi, her bir adımın kritik olduğu wafer temizleme, konumlandırma, kesme, temizleme, inceleme ve sıralama işlemlerini içerir. Otomasyon, lazer kesme ve AI inceleme teknolojilerindeki gelişmelerle birlikte, modern wafer kesme sistemleri daha yüksek hassasiyet, hız ve daha düşük malzeme kaybı elde edebilir. Gelecekte, lazer ve plazma gibi yeni kesme teknolojileri, giderek daha karmaşık çip tasarımlarının ihtiyaçlarını karşılamak için geleneksel bıçak kesiminin yerini kademeli olarak alacak ve yarı iletken üretim süreçlerinin gelişimini daha da ileriye taşıyacaktır.
Wafer Kesim Teknolojisi ve Prensipleri
Resimde üç yaygın gofret kesme teknolojisi gösterilmektedir:Bıçakla Kesme,Lazerle kesme, VePlazma küplemeAşağıda bu üç tekniğin detaylı bir analizi ve tamamlayıcı açıklaması yer almaktadır:
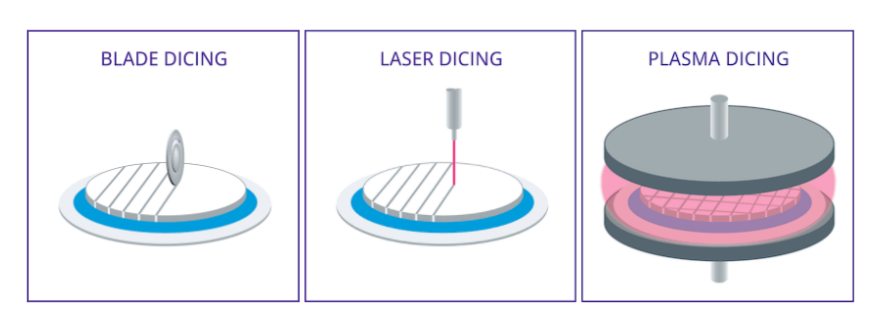
Yarı iletken üretiminde, yonga kesimi, yonganın kalınlığına göre uygun kesme yönteminin seçilmesini gerektiren önemli bir adımdır. İlk adım, yonganın kalınlığını belirlemektir. Yonga kalınlığı 100 mikronu aşarsa, kesme yöntemi olarak bıçak kesme seçilebilir. Bıçak kesme uygun değilse, hem çizici kesme hem de bıçak kesme tekniklerini içeren kırık kesme yöntemi kullanılabilir.
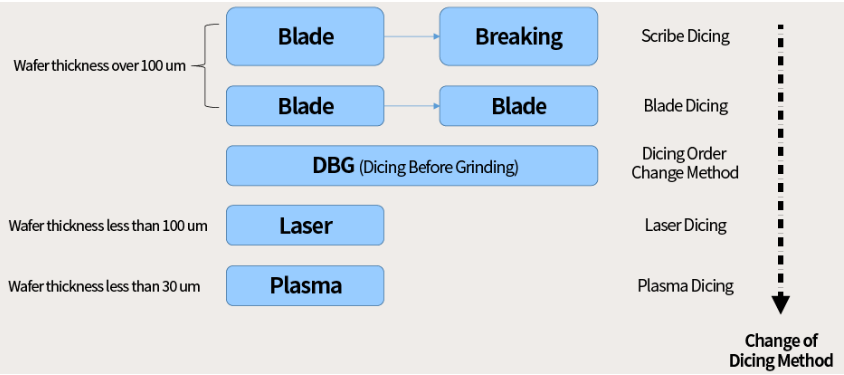
Wafer kalınlığı 30 ila 100 mikron arasında olduğunda, DBG (Dice Before Grinding) yöntemi önerilir. Bu durumda, en iyi sonuçları elde etmek için çizici kesim, bıçakla kesme veya kesme sırasını gerektiği gibi ayarlama seçilebilir.
30 mikrondan daha az kalınlığa sahip ultra ince gofretler için, lazer kesim, aşırı hasara neden olmadan ince gofretleri hassas bir şekilde kesebilme yeteneği nedeniyle tercih edilen yöntem haline gelir. Lazer kesim belirli gereksinimleri karşılayamıyorsa, plazma kesimi alternatif olarak kullanılabilir. Bu akış şeması, farklı kalınlık koşulları altında en uygun gofret kesme teknolojisinin seçilmesini sağlamak için net bir karar verme yolu sunar.
2.1 Mekanik Kesim Teknolojisi
Mekanik kesme teknolojisi, gofret kesmede geleneksel yöntemdir. Temel prensip, gofreti kesmek için kesme aracı olarak yüksek hızlı dönen bir elmas taşlama tekerleği kullanmaktır. Ana ekipman, elmas taşlama tekerleği aracını yüksek hızlarda tahrik ederek önceden tanımlanmış bir kesme yolu boyunca hassas kesme veya kanal açma işlemini gerçekleştiren bir hava yataklı mil içerir. Bu teknoloji, düşük maliyeti, yüksek verimliliği ve geniş uygulanabilirliği nedeniyle endüstride yaygın olarak kullanılmaktadır.
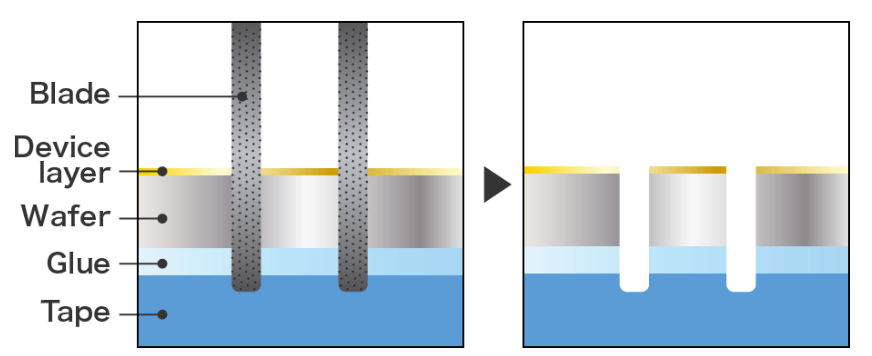
Avantajları
Elmas taşlama tekerleği takımlarının yüksek sertliği ve aşınma direnci, mekanik kesme teknolojisinin geleneksel silikon bazlı malzemeler veya daha yeni bileşik yarı iletkenler olsun, çeşitli gofret malzemelerinin kesme ihtiyaçlarına uyum sağlamasını sağlar. Kullanımı basittir ve nispeten düşük teknik gereksinimlere sahiptir, bu da seri üretimdeki popülerliğini daha da artırır. Ayrıca, lazer kesim gibi diğer kesme yöntemleriyle karşılaştırıldığında, mekanik kesme daha kontrol edilebilir maliyetlere sahiptir ve bu da onu yüksek hacimli üretim ihtiyaçları için uygun hale getirir.
Sınırlamalar
Çok sayıda avantajına rağmen, mekanik kesme teknolojisinin de sınırlamaları vardır. Birincisi, takım ile yonga arasındaki fiziksel temas nedeniyle, kesme hassasiyeti nispeten sınırlıdır ve bu da genellikle sonraki talaş paketleme ve testlerinin doğruluğunu etkileyebilecek boyutsal sapmalara yol açar. İkincisi, mekanik kesme işlemi sırasında kolayca talaş ve çatlak gibi kusurlar oluşabilir ve bu sadece verim oranını etkilemekle kalmaz, aynı zamanda talaşların güvenilirliğini ve kullanım ömrünü de olumsuz etkileyebilir. Mekanik stres kaynaklı hasar, özellikle bu sorunların daha belirgin olduğu kırılgan malzemeleri keserken, yüksek yoğunluklu talaş üretimi için özellikle zararlıdır.
Teknolojik İyileştirmeler
Bu sınırlamaların üstesinden gelmek için araştırmacılar mekanik kesme sürecini sürekli olarak optimize ediyorlar. Temel iyileştirmeler arasında kesme hassasiyetini ve dayanıklılığını iyileştirmek için taşlama tekerleklerinin tasarımını ve malzeme seçimini geliştirmek yer alıyor. Ek olarak, kesme ekipmanının yapısal tasarımını ve kontrol sistemlerini optimize etmek, kesme sürecinin kararlılığını ve otomasyonunu daha da iyileştirdi. Bu gelişmeler, insan operasyonlarından kaynaklanan hataları azaltır ve kesimlerin tutarlılığını iyileştirir. Kesme işlemi sırasında anormalliklerin gerçek zamanlı izlenmesi için gelişmiş denetim ve kalite kontrol teknolojilerinin tanıtılması, kesme güvenilirliğini ve verimini de önemli ölçüde iyileştirdi.
Gelecekteki Gelişim ve Yeni Teknolojiler
Mekanik kesme teknolojisi hala gofret kesmede önemli bir konuma sahip olsa da, yarı iletken süreçleri geliştikçe yeni kesme teknolojileri hızla ilerlemektedir. Örneğin, termal lazer kesme teknolojisinin uygulanması, mekanik kesmedeki hassasiyet ve kusur sorunlarına yeni çözümler sunmaktadır. Bu temassız kesme yöntemi, gofret üzerindeki fiziksel stresi azaltarak, özellikle daha kırılgan malzemeleri keserken, kırılma ve çatlama olayını önemli ölçüde düşürür. Gelecekte, mekanik kesme teknolojisinin yeni kesme teknikleriyle bütünleştirilmesi, yarı iletken üretimine daha fazla seçenek ve esneklik sağlayacak ve üretim verimliliğini ve çip kalitesini daha da artıracaktır.
Sonuç olarak, mekanik kesme teknolojisinin bazı dezavantajları olmasına rağmen, sürekli teknolojik gelişmeler ve yeni kesme teknikleriyle entegrasyonu, yarı iletken üretiminde önemli bir rol oynamasını ve gelecekteki süreçlerde rekabet gücünü korumasını sağlamaktadır.
2.2 Lazer Kesim Teknolojisi
Lazer kesim teknolojisi, yonga kesmede yeni bir yöntem olarak, yüksek hassasiyeti, mekanik temas hasarının olmaması ve hızlı kesim yetenekleri nedeniyle yarı iletken endüstrisinde giderek yaygın ilgi görmektedir. Bu teknoloji, yonga malzemesinin yüzeyinde küçük bir ısıdan etkilenen bölge oluşturmak için bir lazer ışınının yüksek enerji yoğunluğunu ve odaklanma yeteneğini kullanır. Lazer ışını yongaya uygulandığında, oluşan termal stres malzemenin belirlenen noktada kırılmasına neden olarak hassas kesim elde eder.
Lazer Kesim Teknolojisinin Avantajları
• Yüksek Hassasiyet:Lazer ışınının hassas konumlandırma yeteneği, mikron hatta nanometre düzeyinde kesim hassasiyetine olanak vererek, modern yüksek hassasiyetli, yüksek yoğunluklu entegre devre üretiminin gereksinimlerini karşılar.
• Mekanik Temas Yok: Lazer kesim, yonga ile fiziksel teması önleyerek, mekanik kesimde sıkça karşılaşılan kırılma ve çatlama gibi sorunların önüne geçer, yongaların verimini ve güvenilirliğini önemli ölçüde artırır.
• Hızlı Kesim Hızı:Lazer kesimin yüksek hızı, üretim verimliliğinin artmasına katkıda bulunur ve özellikle büyük ölçekli, yüksek hızlı üretim senaryoları için uygundur.
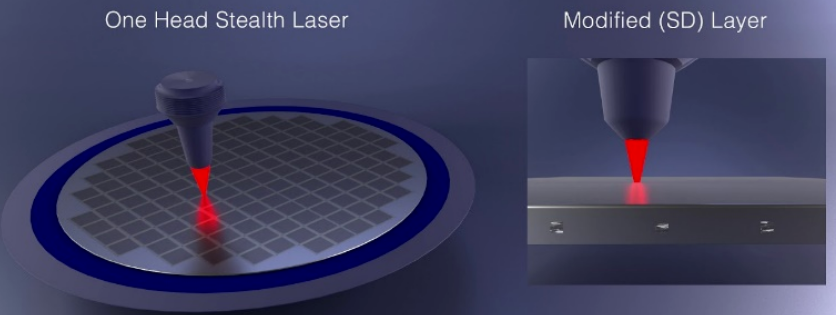
Karşılaşılan Zorluklar
• Yüksek Ekipman Maliyeti: Lazer kesim ekipmanlarının ilk yatırım maliyeti yüksektir, bu durum özellikle küçük ve orta ölçekli üretim işletmeleri için ekonomik baskı oluşturmaktadır.
• Karmaşık Proses Kontrolü: Lazer kesim, enerji yoğunluğu, odak konumu ve kesme hızı gibi çeşitli parametrelerin hassas bir şekilde kontrol edilmesini gerektirdiğinden, süreci karmaşık hale getirir.
• Isıdan Etkilenen Bölge Sorunları: Lazer kesiminin temassız yapısı mekanik hasarı azaltsa da, ısıdan etkilenen bölgenin (HAZ) neden olduğu termal stres, gofret malzemesinin özelliklerini olumsuz etkileyebilir. Bu etkiyi en aza indirmek için sürecin daha fazla optimize edilmesi gerekir.
Teknolojik İyileştirme Yönleri
Bu zorlukların üstesinden gelmek için araştırmacılar ekipman maliyetlerini düşürmeye, kesme verimliliğini artırmaya ve süreç akışını optimize etmeye odaklanıyor.
• Verimli Lazerler ve Optik Sistemler:Daha verimli lazerler ve gelişmiş optik sistemler geliştirilerek, kesim hassasiyeti ve hızı artırılırken ekipman maliyetleri düşürülebilmektedir.
• Proses Parametrelerinin Optimize Edilmesi: Lazerler ve gofret malzemeleri arasındaki etkileşime ilişkin derinlemesine araştırmalar yürütülerek, ısıdan etkilenen bölgeyi azaltan ve dolayısıyla kesim kalitesini artıran prosesler geliştirilmektedir.
• Akıllı Kontrol Sistemleri:Akıllı kontrol teknolojilerinin geliştirilmesi, lazer kesim sürecinin otomatikleştirilmesini ve optimize edilmesini, kararlılığının ve tutarlılığının artırılmasını amaçlamaktadır.
Lazer kesim teknolojisi özellikle ultra ince gofretler ve yüksek hassasiyetli kesim senaryolarında etkilidir. Gofret boyutları arttıkça ve devre yoğunlukları yükseldikçe, geleneksel mekanik kesim yöntemleri modern yarı iletken üretiminin yüksek hassasiyet ve yüksek verimlilik taleplerini karşılamakta zorlanmaktadır. Benzersiz avantajları nedeniyle, lazer kesim bu alanlarda tercih edilen çözüm haline gelmektedir.
Lazer kesim teknolojisi hala yüksek ekipman maliyetleri ve işlem karmaşıklığı gibi zorluklarla karşı karşıya olsa da, yüksek hassasiyet ve temassız hasardaki benzersiz avantajları onu yarı iletken üretiminde önemli bir gelişme yönü haline getirir. Lazer teknolojisi ve akıllı kontrol sistemleri gelişmeye devam ettikçe, lazer kesiminin yarı iletken endüstrisinin sürekli gelişimini yönlendirerek, gofret kesim verimliliğini ve kalitesini daha da iyileştirmesi beklenmektedir.
2.3 Plazma Kesim Teknolojisi
Plazma kesme teknolojisi, yeni ortaya çıkan bir yonga kesme yöntemi olarak son yıllarda önemli ilgi görmüştür. Bu teknoloji, plazma ışınının enerjisini, hızını ve kesme yolunu kontrol ederek yongaları hassas bir şekilde kesmek için yüksek enerjili plazma ışınlarını kullanır ve optimum kesme sonuçları elde eder.
Çalışma Prensibi ve Avantajları
Plazma kesme işlemi, ekipman tarafından üretilen yüksek sıcaklıklı, yüksek enerjili bir plazma ışınına dayanır. Bu ışın, çok kısa bir sürede gofret malzemesini erime veya buharlaşma noktasına kadar ısıtabilir ve bu da hızlı kesmeyi mümkün kılar. Geleneksel mekanik veya lazer kesime kıyasla, plazma kesimi daha hızlıdır ve daha küçük bir ısıdan etkilenen bölge oluşturarak, kesme sırasında çatlakların ve hasarların oluşumunu etkili bir şekilde azaltır.
Pratik uygulamalarda, plazma kesme teknolojisi özellikle karmaşık şekillere sahip gofretleri işlemede ustadır. Yüksek enerjili, ayarlanabilir plazma ışını düzensiz şekilli gofretleri yüksek hassasiyetle kolayca kesebilir. Bu nedenle, mikroelektronik üretiminde, özellikle özelleştirilmiş ve küçük parti yüksek kaliteli çip üretiminde, bu teknoloji yaygın kullanım için büyük bir umut vaat ediyor.
Zorluklar ve Sınırlamalar
Plazma kesim teknolojisi pek çok avantajının yanı sıra bazı zorluklarla da karşı karşıyadır.
• Karmaşık Süreç: Plazma kesme işlemi karmaşıktır ve yüksek hassasiyetli ekipman ve deneyimli operatörler gerektirir.Kesimde doğruluk ve stabilite.
• Çevre Kontrolü ve Güvenliği:Plazma ışınının yüksek sıcaklık ve yüksek enerjili yapısı, sıkı çevre kontrolü ve güvenlik önlemlerini gerektirir; bu da uygulama karmaşıklığını ve maliyetini artırır.
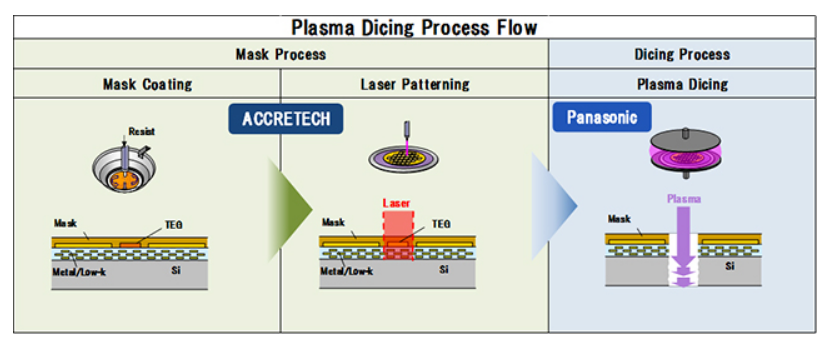
Gelecekteki Gelişim Yönleri
Teknolojik gelişmelerle birlikte, plazma kesimiyle ilişkili zorlukların kademeli olarak üstesinden gelinmesi bekleniyor. Daha akıllı ve daha kararlı kesme ekipmanları geliştirilerek, manuel operasyonlara olan bağımlılık azaltılabilir ve böylece üretim verimliliği artırılabilir. Aynı zamanda, işlem parametrelerini ve kesme ortamını optimize etmek, güvenlik risklerini ve operasyonel maliyetleri düşürmeye yardımcı olacaktır.
Yarı iletken endüstrisinde, yonga kesme ve kesme teknolojisindeki yenilikler, endüstrinin gelişimini yönlendirmek için hayati öneme sahiptir. Yüksek hassasiyeti, verimliliği ve karmaşık yonga şekillerini işleme yeteneğiyle plazma kesme teknolojisi, bu alanda önemli bir yeni oyuncu olarak ortaya çıkmıştır. Bazı zorluklar devam etse de, bu sorunlar, yarı iletken üretimine daha fazla olasılık ve fırsat getiren sürekli teknolojik yeniliklerle kademeli olarak ele alınacaktır.
Plazma kesme teknolojisinin uygulama beklentileri çok geniştir ve gelecekte yarı iletken üretiminde daha önemli bir rol oynaması beklenmektedir. Sürekli teknolojik yenilik ve optimizasyon sayesinde plazma kesme yalnızca mevcut zorlukları ele almakla kalmayacak, aynı zamanda yarı iletken endüstrisinin büyümesinin güçlü bir itici gücü haline gelecektir.
2.4 Kesim Kalitesi ve Etkileyen Faktörler
Wafer kesme kalitesi, sonraki yonga paketleme, test etme ve nihai ürünün genel performansı ve güvenilirliği için kritik öneme sahiptir. Kesme sırasında karşılaşılan yaygın sorunlar arasında çatlaklar, kırılma ve kesme sapmaları bulunur. Bu sorunlar, birlikte çalışan birkaç faktörden etkilenir.
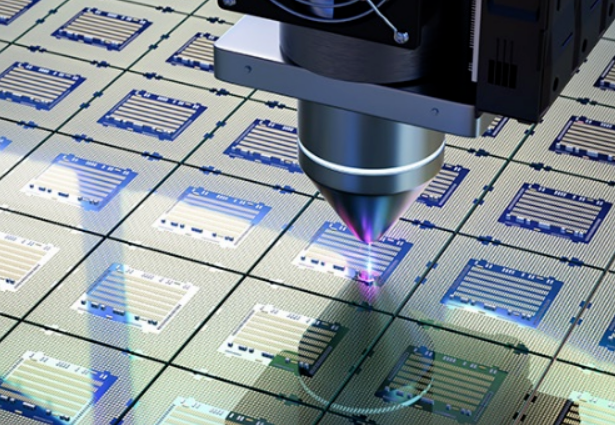
Kategori | İçerik | Darbe |
İşlem Parametreleri | Kesme hızı, ilerleme hızı ve kesme derinliği, kesme işleminin kararlılığını ve hassasiyetini doğrudan etkiler. Uygunsuz ayarlar, gerilim yoğunlaşmasına ve aşırı ısıdan etkilenen bölgeye yol açabilir ve bu da çatlaklara ve kırılmalara neden olabilir. İstenilen kesme sonuçlarına ulaşmak için, parametrelerin wafer malzemesi, kalınlık ve kesme gereksinimlerine göre uygun şekilde ayarlanması önemlidir. | Doğru proses parametreleri hassas kesimi garanti altına alır ve çatlak, kırılma gibi kusurların oluşma riskini azaltır. |
Ekipman ve Malzeme Faktörleri | -Bıçak Kalitesi: Bıçağın malzemesi, sertliği ve aşınma direnci, kesme işleminin düzgünlüğünü ve kesilen yüzeyin düzlüğünü etkiler. Düşük kaliteli bıçaklar sürtünmeyi ve termal stresi artırarak çatlaklara veya kırılmalara yol açabilir. Doğru bıçak malzemesini seçmek çok önemlidir. -Soğutma Sıvısı Performansı: Soğutma sıvıları kesme sıcaklığını düşürmeye, sürtünmeyi en aza indirmeye ve döküntüleri temizlemeye yardımcı olur. Etkisiz soğutma sıvıları yüksek sıcaklıklara ve döküntü birikmesine yol açarak kesme kalitesini ve verimliliğini etkileyebilir. Verimli ve çevre dostu soğutma sıvılarını seçmek hayati önem taşır. | Bıçak kalitesi, kesimin hassasiyetini ve pürüzsüzlüğünü etkiler. Etkisiz soğutma sıvısı, düşük kesme kalitesi ve verimliliğiyle sonuçlanabilir ve bu da optimum soğutma sıvısı kullanımına olan ihtiyacı vurgular. |
Proses Kontrolü ve Kalite Denetimi | -Proses Kontrolü: Kesme sürecinde istikrar ve tutarlılığı sağlamak için önemli kesme parametrelerinin gerçek zamanlı izlenmesi ve ayarlanması. -Kalite Denetimi: Kesim sonrası görünüm kontrolleri, boyut ölçümleri ve elektriksel performans testleri, kalite sorunlarının derhal belirlenmesine ve çözülmesine yardımcı olarak kesim doğruluğunu ve tutarlılığını artırır. | Uygun proses kontrolü ve kalite denetimi, tutarlı, yüksek kaliteli kesme sonuçlarının sağlanmasına ve potansiyel sorunların erken tespit edilmesine yardımcı olur. |

Kesim Kalitesini İyileştirme
Kesim kalitesini iyileştirmek, proses parametreleri, ekipman ve malzeme seçimi, proses kontrolü ve denetimi hesaba katan kapsamlı bir yaklaşım gerektirir. Kesim teknolojilerini sürekli olarak iyileştirerek ve proses yöntemlerini optimize ederek, wafer kesiminin hassasiyeti ve kararlılığı daha da artırılabilir ve yarı iletken üretim endüstrisi için daha güvenilir teknik destek sağlanabilir.
#03 Kesim Sonrası Taşıma ve Test
3.1 Temizleme ve Kurutma
Yonga kesimi sonrasındaki temizleme ve kurutma adımları, talaş kalitesini ve sonraki işlemlerin sorunsuz ilerlemesini sağlamak için kritik öneme sahiptir. Bu aşamada, kesme sırasında oluşan silikon artıklarını, soğutma sıvısı kalıntılarını ve diğer kirleticileri iyice temizlemek önemlidir. Temizleme işlemi sırasında talaşların zarar görmemesini sağlamak ve kurutma işleminden sonra korozyon veya elektrostatik deşarj gibi sorunları önlemek için talaş yüzeyinde nem kalmamasını sağlamak da aynı derecede önemlidir.
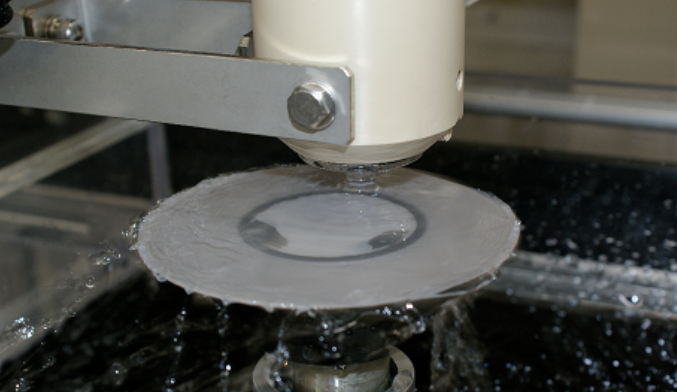
Kesim Sonrası İşleme: Temizleme ve Kurutma İşlemi
İşlem Adımı | İçerik | Darbe |
Temizleme İşlemi | -Yöntem:Temizlik için özel temizlik maddeleri ve saf su kullanın, bunu ultrasonik veya mekanik fırçalama teknikleriyle birleştirin. | Kirleticilerin tamamen uzaklaştırılmasını sağlar ve temizlik sırasında talaşların zarar görmesini önler. |
-Temizlik Maddesi Seçimi:Çipe zarar vermeden etkili bir temizlik sağlamak için yonga malzemesine ve kirletici türüne göre seçim yapın. | Etkili temizlik ve talaş koruması için doğru temizlik maddesinin seçimi çok önemlidir. | |
-Parametre Kontrolü: Kalite sorunlarının yanlış temizlikten kaynaklanmasını önlemek için temizlik sıcaklığını, süresini ve temizlik solüsyonu konsantrasyonunu sıkı bir şekilde kontrol edin. | Kontroller, gofretin hasar görmesini veya geride kirletici maddelerin kalmasını önlemeye yardımcı olarak tutarlı kaliteyi garanti eder. | |
Kurutma İşlemi | -Geleneksel Yöntemler: Düşük verimliliğe sahip olup statik elektrik oluşumuna yol açabilen doğal hava kurutma ve sıcak hava kurutma. | Kuruma sürelerinin yavaşlamasına ve potansiyel statik sorunlara yol açabilir. |
-Modern Teknolojiler:Çiplerin çabuk kurumasını ve zararlı etkilerden korunmasını sağlamak için vakumlu kurutma ve kızılötesi kurutma gibi ileri teknolojiler kullanın. | Daha hızlı ve daha etkili kurutma işlemi, statik deşarj veya nem kaynaklı sorunların riskini azaltır. | |
Ekipman Seçimi ve Bakımı | -Ekipman Seçimi: Yüksek performanslı temizleme ve kurutma makineleri, işleme verimliliğini artırır ve elleçleme sırasında ortaya çıkabilecek sorunları hassas bir şekilde kontrol eder. | Yüksek kaliteli makineler daha iyi işlemeyi garanti eder ve temizleme ve kurutma sırasında hata olasılığını azaltır. |
-Ekipman Bakımı: Ekipmanın düzenli olarak denetlenmesi ve bakımı, optimum çalışma koşullarında kalmasını sağlayarak çip kalitesini garanti eder. | Uygun bakım, ekipman arızalarını önleyerek güvenilir ve yüksek kaliteli işlemeyi garanti eder. |
Kesim Sonrası Temizlik ve Kurutma
Wafer kesimi sonrası temizleme ve kurutma adımları, nihai işleme sonucunu garantilemek için birden fazla faktörün dikkatli bir şekilde değerlendirilmesini gerektiren karmaşık ve hassas süreçlerdir. Bilimsel yöntemler ve titiz prosedürler kullanılarak, her çipin sonraki paketleme ve test aşamalarına en iyi durumda girmesini sağlamak mümkündür.
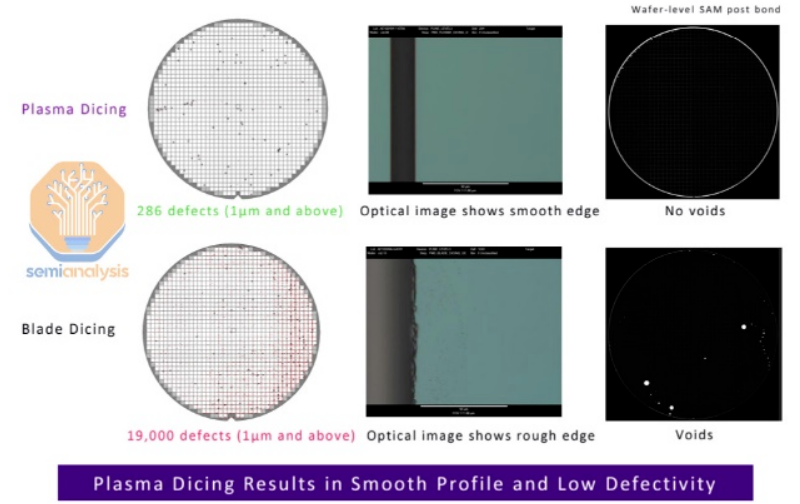
Kesim Sonrası Muayene ve Test
Adım | İçerik | Darbe |
Muayene Adımı | 1.Görsel Muayene: Çatlaklar, kırılmalar veya talaş yüzeyindeki kirlenmeler gibi görünür kusurları kontrol etmek için görsel veya otomatik muayene ekipmanı kullanın. Atığı önlemek için fiziksel olarak hasarlı talaşları hızla belirleyin. | Arızalı talaşların sürecin erken aşamalarında tespit edilip ortadan kaldırılmasına yardımcı olarak malzeme kaybını azaltır. |
2.Beden Ölçümü:Talaş boyutlarını doğru bir şekilde ölçmek için hassas ölçüm cihazları kullanın, böylece kesim boyutunun tasarım özelliklerine uygun olduğundan emin olun ve performans sorunlarının veya paketleme zorluklarının önüne geçin. | Çiplerin gerekli boyut sınırları içerisinde olmasını sağlayarak performans düşüşünü veya montaj sorunlarını önler. | |
3.Elektriksel Performans Testi: Direnç, kapasitans ve endüktans gibi temel elektriksel parametreleri değerlendirerek uyumsuz yongaları belirleyin ve yalnızca performans açısından yeterli olan yongaların bir sonraki aşamaya geçmesini sağlayın. | Sadece işlevsel ve performans testleri yapılmış yongaların süreçte ilerlemesini sağlayarak, sonraki aşamalarda arıza riskini azaltır. | |
Test Adımı | 1.Fonksiyonel Test:Çipin temel işlevselliğinin amaçlandığı gibi çalıştığını doğrulayın, işlevsel anormallikleri olan çipleri belirleyin ve eleyin. | Daha sonraki aşamalara geçmeden önce çiplerin temel operasyonel gereksinimlerini karşıladığından emin olur. |
2.Güvenilirlik Testi: Uzun süreli kullanım veya zorlu ortamlarda çip performansının kararlılığını değerlendirin; bu genellikle yüksek sıcaklıkta yaşlanma, düşük sıcaklıkta test ve gerçek dünyadaki aşırı koşulları simüle etmek için nem testini içerir. | Çiplerin çeşitli çevre koşullarında güvenilir bir şekilde çalışmasını sağlayarak ürünün ömrünü ve kararlılığını artırır. | |
3.Uyumluluk Testi: Çipin diğer bileşenlerle veya sistemlerle düzgün bir şekilde çalıştığını doğrulayın, uyumsuzluk nedeniyle herhangi bir arıza veya performans düşüşü olmadığından emin olun. | Uyumluluk sorunlarını önleyerek gerçek dünya uygulamalarında sorunsuz çalışmayı sağlar. |
3.3 Paketleme ve Depolama
Yonga kesimi sonrasında yongalar, yarı iletken üretim sürecinin önemli bir çıktısıdır ve bunların paketlenmesi ve depolanması aşamaları da aynı derecede önemlidir. Uygun paketleme ve depolama önlemleri, yalnızca yongaların nakliye ve depolanması sırasında güvenliğini ve kararlılığını sağlamak için değil, aynı zamanda sonraki üretim, test ve paketleme aşamaları için güçlü destek sağlamak için de önemlidir.
Muayene ve Test Aşamalarının Özeti:
Yonga kesimi sonrası yongalar için inceleme ve test adımları, görsel inceleme, boyut ölçümü, elektriksel performans testi, işlevsel test, güvenilirlik testi ve uyumluluk testi gibi bir dizi yönü kapsar. Bu adımlar birbiriyle bağlantılı ve tamamlayıcıdır ve ürün kalitesini ve güvenilirliğini sağlamak için sağlam bir bariyer oluşturur. Sıkı inceleme ve test prosedürleri aracılığıyla, olası sorunlar derhal belirlenebilir ve çözülebilir ve nihai ürünün müşteri gereksinimlerini ve beklentilerini karşılaması sağlanır.
Bakış açısı | İçerik |
Paketleme Önlemleri | 1.Anti-statik:Ambalaj malzemeleri, statik elektriğin cihazlara zarar vermesini veya performanslarını etkilemesini önlemek için mükemmel anti-statik özelliklere sahip olmalıdır. |
2.Nem geçirmez:Ambalaj malzemelerinin neme karşı dayanıklılığının iyi olması, nemin neden olduğu korozyonu ve elektriksel performansın bozulmasını önlemelidir. | |
3.Darbeye dayanıklı: Paketleme malzemeleri, talaşları nakliye sırasında titreşim ve darbelerden korumak için etkili bir şok emilimi sağlamalıdır. | |
Depolama Ortamı | 1.Nem Kontrolü: Aşırı nemden kaynaklanan nem emilimini ve korozyonu veya düşük nemden kaynaklanan statik sorunları önlemek için nemi uygun aralıkta sıkı bir şekilde kontrol edin. |
2.Temizlik: Toz ve yabancı maddelerin talaşları kirletmesini önlemek için temiz bir depolama ortamı sağlayın. | |
3.Sıcaklık Kontrolü: Aşırı ısınma veya düşük sıcaklıklardan kaynaklanan yoğuşma sorunları nedeniyle oluşan hızlandırılmış eskimeyi önlemek için makul bir sıcaklık aralığı belirleyin ve sıcaklık stabilitesini koruyun. | |
Düzenli Muayene | Olası sorunları zamanında belirlemek ve gidermek için görsel incelemeler, boyut ölçümleri ve elektrik performans testleri kullanarak depolanan yongaları düzenli olarak inceleyin ve değerlendirin. Depolama süresi ve koşullarına göre, yongaların optimum durumda kullanılmasını sağlamak için kullanımını planlayın. |
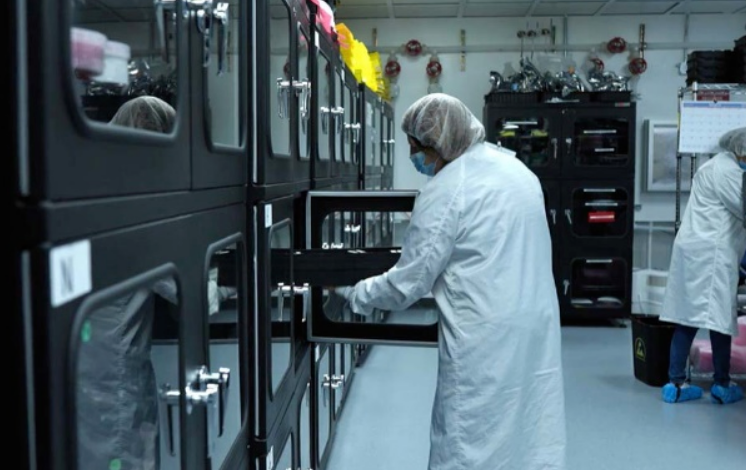
Yarı iletken üretiminde, yonga kesme işlemi sırasında oluşan mikro çatlaklar ve hasar sorunu önemli bir zorluktur. Kesme gerilimi, yonga yüzeyinde küçük çatlaklar ve hasarlar oluşturarak üretim maliyetlerinin artmasına ve ürün kalitesinin düşmesine yol açtığı için bu olgunun birincil nedenidir.
Bu zorluğun üstesinden gelmek için, kesme stresini en aza indirmek ve optimize edilmiş kesme teknikleri, araçları ve koşulları uygulamak hayati önem taşır. Bıçak malzemesi, kesme hızı, basınç ve soğutma yöntemleri gibi faktörlere dikkat etmek, mikro çatlakların oluşumunu azaltmaya ve işlemin genel verimini iyileştirmeye yardımcı olabilir. Ayrıca, lazer kesme gibi daha gelişmiş kesme teknolojilerine yönelik devam eden araştırmalar, bu sorunları daha da azaltmanın yollarını araştırmaktadır.
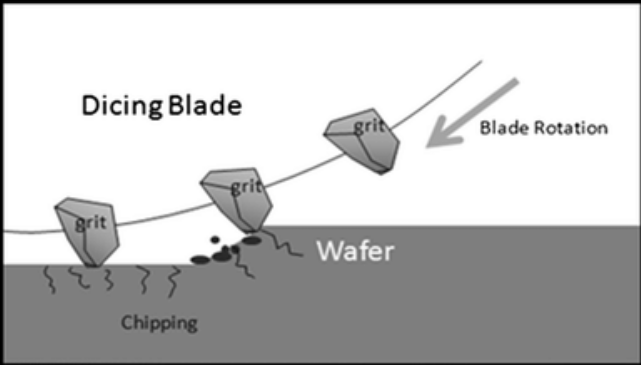
Kırılgan bir malzeme olan gofretler, mekanik, termal veya kimyasal strese maruz kaldığında iç yapısal değişikliklere eğilimlidir ve bu da mikro çatlakların oluşmasına yol açar. Bu çatlaklar hemen fark edilmese de, üretim süreci ilerledikçe genişleyebilir ve daha ciddi hasara neden olabilir. Bu sorun, sıcaklık dalgalanmalarının ve ek mekanik streslerin bu mikro çatlakların görünür kırıklara dönüşmesine ve potansiyel olarak çip arızasına yol açabileceği sonraki paketleme ve test aşamalarında özellikle sorunlu hale gelir.
Bu riski azaltmak için, kesme hızı, basınç ve sıcaklık gibi parametreleri optimize ederek kesme işlemini dikkatli bir şekilde kontrol etmek esastır. Lazer kesme gibi daha az agresif kesme yöntemleri kullanmak, gofret üzerindeki mekanik stresi azaltabilir ve mikro çatlakların oluşumunu en aza indirebilir. Ayrıca, gofret kesme işlemi sırasında kızılötesi tarama veya X-ışını görüntüleme gibi gelişmiş inceleme yöntemlerinin uygulanması, daha fazla hasara yol açmadan önce bu erken aşamadaki çatlakların tespit edilmesine yardımcı olabilir.
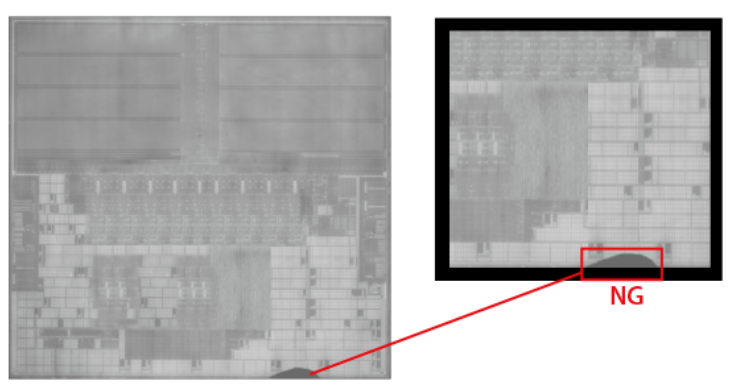
Wafer yüzeyindeki hasar, çipin performansı ve güvenilirliği üzerinde doğrudan bir etkiye sahip olabileceğinden, kesme işleminde önemli bir endişe kaynağıdır. Bu tür hasarlar, kesme araçlarının yanlış kullanımı, yanlış kesme parametreleri veya wafer'ın kendisinde bulunan malzeme kusurlarından kaynaklanabilir. Nedeni ne olursa olsun, bu hasarlar devrenin elektrik direncinde veya kapasitansında değişikliklere yol açarak genel performansı etkileyebilir.
Bu sorunları çözmek için iki temel strateji araştırılıyor:
1.Kesici takımların ve parametrelerin optimize edilmesi:Daha keskin bıçaklar kullanarak, kesme hızını ayarlayarak ve kesme derinliğini değiştirerek, kesme işlemi sırasında oluşan stres yoğunlaşması en aza indirilebilir ve böylece hasar olasılığı azaltılabilir.
2.Yeni kesme teknolojilerini keşfetmek: Lazer kesim ve plazma kesim gibi gelişmiş teknikler, potansiyel olarak gofrete verilen hasar seviyesini azaltırken gelişmiş hassasiyet sunar. Bu teknolojiler, gofret üzerindeki termal ve mekanik stresi en aza indirirken yüksek kesim doğruluğu elde etmenin yollarını bulmak için incelenmektedir.
Isıl Etki Alanı ve Performans Üzerindeki Etkileri
Lazer ve plazma kesme gibi termal kesme işlemlerinde, yüksek sıcaklıklar kaçınılmaz olarak gofretin yüzeyinde termal bir etki bölgesi yaratır. Sıcaklık gradyanının önemli olduğu bu alan, malzemenin özelliklerini değiştirebilir ve çipin nihai performansını etkileyebilir.
Termal Etkilenen Bölgenin (TAZ) Etkisi:
Kristal Yapı Değişiklikleri: Yüksek sıcaklıklarda, yonga malzemesi içindeki atomlar yeniden düzenlenebilir ve kristal yapıda bozulmalara neden olabilir. Bu bozulma, malzemeyi zayıflatır, mekanik mukavemetini ve kararlılığını azaltır ve bu da kullanım sırasında çip arızası riskini artırır.
Elektriksel Özelliklerdeki Değişiklikler: Yüksek sıcaklıklar, yarı iletken malzemelerdeki taşıyıcı konsantrasyonunu ve hareketliliğini değiştirebilir, çipin elektriksel iletkenliğini ve akım iletim verimliliğini etkileyebilir. Bu değişiklikler çip performansında düşüşe yol açabilir ve potansiyel olarak çipi amaçlanan amacına uygunsuz hale getirebilir.
Bu etkileri azaltmak için, kesme sırasında sıcaklığı kontrol etmek, kesme parametrelerini optimize etmek ve soğutma jetleri veya işlem sonrası işlemler gibi yöntemleri araştırmak, termal etkinin kapsamını azaltmak ve malzeme bütünlüğünü korumak için gerekli stratejilerdir.
Genel olarak, hem mikro çatlaklar hem de termal darbe bölgeleri, wafer kesme teknolojisinde önemli zorluklardır. Yarı iletken ürünlerinin kalitesini iyileştirmek ve pazar rekabet güçlerini artırmak için teknolojik ilerlemeler ve kalite kontrol önlemlerinin yanı sıra sürekli araştırma yapılması gerekecektir.
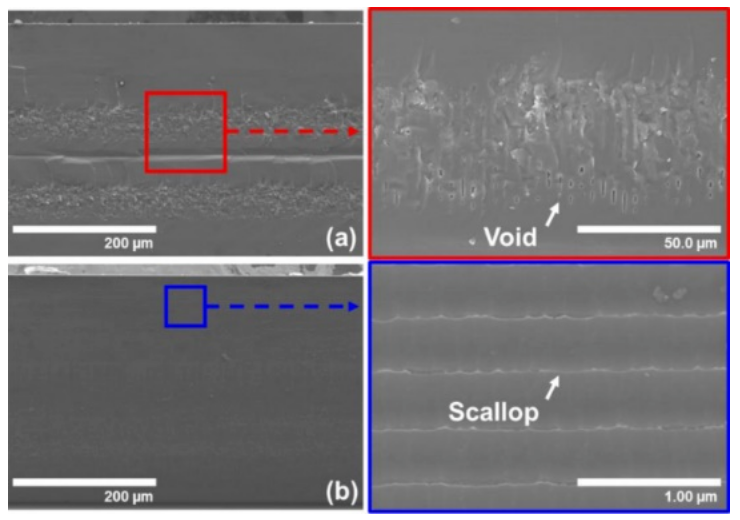
Termal Etki Bölgesini Kontrol Altına Almak İçin Alınacak Önlemler:
Kesme İşlemi Parametrelerinin Optimize Edilmesi: Kesme hızını ve gücünü azaltmak, termal darbe bölgesinin (TAZ) boyutunu etkili bir şekilde en aza indirebilir. Bu, kesme işlemi sırasında üretilen ısı miktarının kontrol edilmesine yardımcı olur ve bu da doğrudan gofretin malzeme özelliklerini etkiler.
Gelişmiş Soğutma Teknolojileri: Sıvı nitrojen soğutma ve mikroakışkan soğutma gibi teknolojilerin uygulanması, termal etki bölgesinin aralığını önemli ölçüde sınırlayabilir. Bu soğutma yöntemleri, ısının daha verimli bir şekilde dağıtılmasına yardımcı olur, böylece gofretin malzeme özellikleri korunur ve termal hasar en aza indirilir.
Malzeme Seçimi: Araştırmacılar, mükemmel termal iletkenliğe ve mekanik dayanıklılığa sahip karbon nanotüpler ve grafen gibi yeni malzemeler araştırıyorlar. Bu malzemeler, çiplerin genel performansını iyileştirirken termal darbe bölgesini azaltabilir.
Özetle, termal darbe bölgesi termal kesme teknolojilerinin kaçınılmaz bir sonucu olsa da, optimize edilmiş işleme teknikleri ve malzeme seçimiyle etkili bir şekilde kontrol edilebilir. Gelecekteki araştırmalar muhtemelen daha verimli ve hassas gofret kesme elde etmek için termal kesme süreçlerinin ince ayarını yapmaya ve otomatikleştirmeye odaklanacaktır.

Denge Stratejisi:
Wafer verimi ile üretim verimliliği arasında optimum dengeyi sağlamak, wafer kesme teknolojisinde sürekli bir zorluktur. Üreticilerin, rasyonel bir üretim stratejisi ve süreç parametreleri geliştirmek için pazar talebi, üretim maliyetleri ve ürün kalitesi gibi birden fazla faktörü göz önünde bulundurmaları gerekir. Aynı zamanda, gelişmiş kesme ekipmanlarının tanıtılması, operatör becerilerinin geliştirilmesi ve ham madde kalite kontrolünün iyileştirilmesi, üretim verimliliğini artırırken verimi korumak veya hatta iyileştirmek için önemlidir.
Gelecekteki Zorluklar ve Fırsatlar:
Yarı iletken teknolojisinin ilerlemesiyle birlikte, yonga kesimi yeni zorluklar ve fırsatlarla karşı karşıyadır. Çip boyutları küçüldükçe ve entegrasyon arttıkça, kesme hassasiyeti ve kalitesine yönelik talepler önemli ölçüde artmaktadır. Aynı zamanda, ortaya çıkan teknolojiler yonga kesme tekniklerinin geliştirilmesi için yeni fikirler sunmaktadır. Üreticiler, pazar dinamiklerine ve teknolojik trendlere uyum sağlamalı, pazar değişikliklerini ve teknolojik talepleri karşılamak için üretim stratejilerini ve işlem parametrelerini sürekli olarak ayarlamalı ve optimize etmelidir.
Sonuç olarak, pazar talebi, üretim maliyetleri ve ürün kalitesi gibi hususların bir araya getirilmesi, gelişmiş ekipman ve teknolojinin kullanılması, operatör becerilerinin artırılması ve hammadde kontrolünün güçlendirilmesiyle üreticiler, yonga kesme işlemi sırasında yonga verimi ile üretim verimliliği arasında en iyi dengeyi sağlayabilir ve bu da verimli ve yüksek kaliteli yarı iletken ürün üretimine yol açabilir.
Geleceğe Bakış:
Hızlı teknolojik gelişmelerle, yarı iletken teknolojisi benzeri görülmemiş bir hızla ilerliyor. Yarı iletken üretiminde kritik bir adım olarak, yonga kesme teknolojisi heyecan verici yeni gelişmelere hazır. İleriye bakıldığında, yonga kesme teknolojisinin hassasiyet, verimlilik ve maliyette önemli iyileştirmeler elde etmesi ve yarı iletken endüstrisinin sürekli büyümesine yeni bir canlılık katması bekleniyor.
Hassasiyetin Artırılması:
Daha yüksek hassasiyet arayışında, wafer kesme teknolojisi mevcut süreçlerin sınırlarını sürekli olarak zorlayacaktır. Kesme sürecinin fiziksel ve kimyasal mekanizmalarını derinlemesine inceleyerek ve kesme parametrelerini hassas bir şekilde kontrol ederek, giderek karmaşıklaşan devre tasarımı gereksinimlerini karşılamak için daha ince kesme sonuçları elde edilecektir. Ek olarak, yeni malzemelerin ve kesme yöntemlerinin keşfi, verimi ve kaliteyi önemli ölçüde iyileştirecektir.
Verimliliğin Artırılması:
Yeni gofret kesme ekipmanı akıllı ve otomatik tasarıma odaklanacaktır. Gelişmiş kontrol sistemleri ve algoritmaların tanıtımı, ekipmanın farklı malzemelere ve tasarım gereksinimlerine uyum sağlamak için kesme parametrelerini otomatik olarak ayarlamasını sağlayacak ve böylece üretim verimliliğini önemli ölçüde artıracaktır. Çoklu gofret kesme teknolojisi ve hızlı bıçak değiştirme sistemleri gibi yenilikler, verimliliği artırmada önemli bir rol oynayacaktır.
Maliyetleri Azaltmak:
Maliyetleri azaltmak, gofret kesme teknolojisinin geliştirilmesi için önemli bir yöndür. Yeni malzemeler ve kesme yöntemleri geliştirildikçe, ekipman maliyetleri ve bakım giderlerinin etkili bir şekilde kontrol edilmesi beklenmektedir. Ek olarak, üretim süreçlerini optimize etmek ve hurda oranlarını azaltmak, üretim sırasında atığı daha da azaltacak ve genel üretim maliyetlerinde bir düşüşe yol açacaktır.
Akıllı Üretim ve IoT:
Akıllı üretim ve Nesnelerin İnterneti (IoT) teknolojilerinin entegrasyonu, wafer kesme teknolojisine dönüştürücü değişiklikler getirecektir. Cihazlar arasındaki bağlantı ve veri paylaşımı sayesinde, üretim sürecinin her adımı gerçek zamanlı olarak izlenebilir ve optimize edilebilir. Bu, yalnızca üretim verimliliğini ve ürün kalitesini iyileştirmekle kalmaz, aynı zamanda şirketlere daha doğru pazar tahmini ve karar alma desteği de sağlar.
Gelecekte, wafer kesme teknolojisi hassasiyet, verimlilik ve maliyet açısından kayda değer ilerlemeler kaydedecektir. Bu ilerlemeler, yarı iletken endüstrisinin sürekli gelişimini yönlendirecek ve insan toplumuna daha fazla teknolojik yenilik ve kolaylık getirecektir.
Yayınlanma zamanı: 19-Kas-2024