İPC (İstatistiksel Proses Kontrolü), üretim sürecinde çeşitli aşamaların kararlılığını izlemek, kontrol etmek ve iyileştirmek için kullanılan, yonga üretim sürecinde önemli bir araçtır.
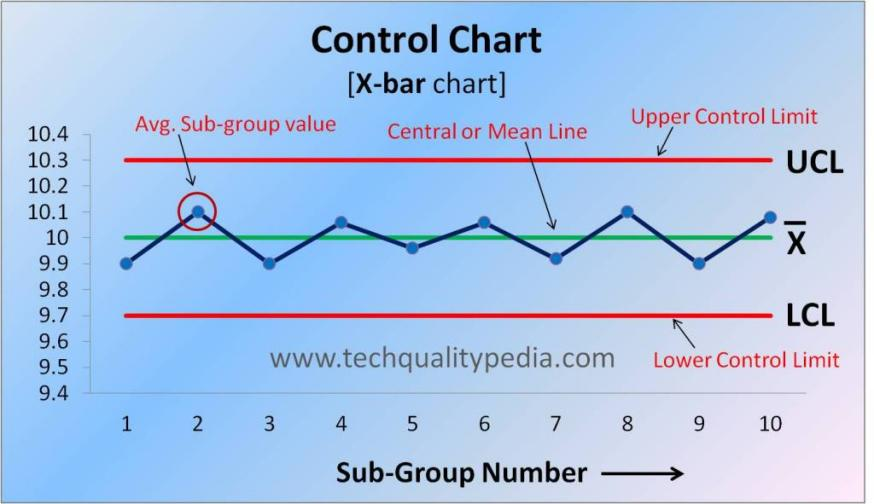
1. SPC Sistemine Genel Bakış
SPC, üretim süreçlerini izlemek ve kontrol etmek için istatistiksel teknikler kullanan bir yöntemdir. Temel işlevi, gerçek zamanlı verileri toplayarak ve analiz ederek üretim sürecindeki anormallikleri tespit etmek ve mühendislerin zamanında ayarlamalar ve kararlar almasına yardımcı olmaktır. SPC'nin amacı, üretim sürecindeki çeşitliliği azaltarak ürün kalitesinin sabit kalmasını ve özelliklere uymasını sağlamaktır.
SPC, aşındırma işleminde şu amaçlarla kullanılır:
Kritik ekipman parametrelerini izleyin (örneğin, aşındırma hızı, RF gücü, oda basıncı, sıcaklık, vb.)
Ana ürün kalite göstergelerini analiz edin (örneğin, çizgi genişliği, aşındırma derinliği, kenar pürüzlülüğü, vb.)
Mühendisler bu parametreleri izleyerek ekipman performansında düşüş veya üretim sürecindeki sapmalara işaret eden eğilimleri tespit edebilir ve böylece hurda oranlarını azaltabilirler.
2. SPC Sisteminin Temel Bileşenleri
SPC sistemi birkaç temel modülden oluşmaktadır:
Veri Toplama Modülü: Ekipman ve proses akışlarından (örneğin FDC, EES sistemleri aracılığıyla) gerçek zamanlı verileri toplar ve önemli parametreleri ve üretim sonuçlarını kaydeder.
Kontrol Tablosu Modülü: Prosesin kontrol altında olup olmadığını belirlemek ve prosesin kararlılığını görselleştirmek için istatistiksel kontrol tablolarını (örneğin, X-Bar tablosu, R tablosu, Cp/Cpk tablosu) kullanır.
Alarm Sistemi: Kritik parametreler kontrol limitlerini aştığında veya trend değişiklikleri gösterdiğinde alarmları tetikleyerek mühendislerin harekete geçmesini sağlar.
Analiz ve Raporlama Modülü: SPC grafiklerine dayalı olarak anormalliklerin temel nedenini analiz eder ve proses ve ekipman için düzenli olarak performans raporları oluşturur.
3. SPC'de Kontrol Grafiklerinin Ayrıntılı Açıklaması
Kontrol çizelgeleri, SPC'de en sık kullanılan araçlardan biridir ve "normal varyasyon" (doğal proses varyasyonlarından kaynaklanan) ile "anormal varyasyon" (ekipman arızaları veya proses sapmalarından kaynaklanan) arasında ayrım yapmaya yardımcı olur. Yaygın kontrol çizelgeleri şunları içerir:
X-Bar ve R Grafikleri: Üretim partileri içindeki ortalama ve aralığı izleyerek sürecin stabil olup olmadığını gözlemlemek için kullanılır.
Cp ve Cpk Endeksleri: Proses kabiliyetini ölçmek için kullanılır, yani proses çıktısının sürekli olarak şartname gereksinimlerini karşılayıp karşılayamayacağını. Cp potansiyel kabiliyeti ölçerken, Cpk proses merkezinin şartname sınırlarından sapmasını dikkate alır.
Örneğin, aşındırma işleminde aşındırma oranı ve yüzey pürüzlülüğü gibi parametreleri izleyebilirsiniz. Belirli bir ekipman parçasının aşındırma oranı kontrol sınırını aşarsa, bunun doğal bir değişim mi yoksa ekipman arızasının bir göstergesi mi olduğunu belirlemek için kontrol grafiklerini kullanabilirsiniz.
4. Aşındırma Ekipmanlarında SPC Uygulaması
Aşındırma işleminde ekipman parametrelerinin kontrolü kritik öneme sahiptir ve SPC, işlem kararlılığının aşağıdaki yollarla iyileştirilmesine yardımcı olur:
Ekipman Durumu İzleme: FDC gibi sistemler, aşındırma ekipmanının temel parametreleri (örneğin, RF gücü, gaz akışı) hakkında gerçek zamanlı veri toplar ve bu verileri SPC kontrol grafikleriyle birleştirerek olası ekipman sorunlarını tespit eder. Örneğin, bir kontrol grafiğindeki RF gücünün ayarlanan değerden kademeli olarak saptığını görürseniz, ürün kalitesini etkilememek için ayarlama veya bakım için erken önlem alabilirsiniz.
Ürün Kalitesi İzleme: Ayrıca, kararlılıklarını izlemek için SPC sistemine önemli ürün kalitesi parametrelerini (örneğin, aşındırma derinliği, çizgi genişliği) girebilirsiniz. Bazı kritik ürün göstergeleri hedef değerlerden kademeli olarak saparsa, SPC sistemi bir alarm vererek işlem ayarlamalarının gerekli olduğunu belirtir.
Önleyici Bakım (PM): SPC, ekipman için önleyici bakım döngüsünü optimize etmeye yardımcı olabilir. Ekipman performansı ve süreç sonuçlarına ilişkin uzun vadeli verileri analiz ederek, ekipman bakımı için en uygun zamanı belirleyebilirsiniz. Örneğin, RF gücünü ve ESC ömrünü izleyerek, temizlik veya bileşen değişiminin ne zaman gerekli olduğunu belirleyebilir, ekipman arıza oranlarını ve üretim duruş süresini azaltabilirsiniz.
5. SPC Sistemi için Günlük Kullanım İpuçları
SPC sisteminin günlük operasyonlarda kullanımında aşağıdaki adımlar izlenebilir:
Ana Kontrol Parametrelerini (KPI) Tanımlayın: Üretim sürecindeki en önemli parametreleri belirleyin ve bunları SPC izlemesine dahil edin. Bu parametreler ürün kalitesi ve ekipman performansıyla yakından ilişkili olmalıdır.
Kontrol Limitleri ve Alarm Limitleri Ayarlayın: Tarihsel verilere ve proses gereksinimlerine dayanarak, her parametre için makul kontrol limitleri ve alarm limitleri ayarlayın. Kontrol limitleri genellikle ±3σ (standart sapmalar) olarak ayarlanırken, alarm limitleri prosesin ve ekipmanın özel koşullarına dayanır.
Sürekli İzleme ve Analiz: Veri eğilimlerini ve varyasyonlarını analiz etmek için SPC kontrol grafiklerini düzenli olarak inceleyin. Bazı parametreler kontrol sınırlarını aşarsa, ekipman parametrelerini ayarlamak veya ekipman bakımı yapmak gibi acil eylem gerekir.
Anormallik Yönetimi ve Kök Neden Analizi: Bir anormallik meydana geldiğinde, SPC sistemi olay hakkında ayrıntılı bilgi kaydeder. Bu bilgilere dayanarak anormalliğin kök nedenini gidermeniz ve analiz etmeniz gerekir. Sorunun ekipman arızasından, proses sapmasından veya dış çevresel faktörlerden kaynaklanıp kaynaklanmadığını analiz etmek için FDC sistemlerinden, EES sistemlerinden vb. verileri birleştirmek sıklıkla mümkündür.
Sürekli İyileştirme: SPC sistemi tarafından kaydedilen geçmiş verileri kullanarak, süreçteki zayıf noktaları belirleyin ve iyileştirme planları önerin. Örneğin, aşındırma sürecinde, ESC ömrünün ve temizleme yöntemlerinin ekipman bakım döngüleri üzerindeki etkisini analiz edin ve ekipman çalışma parametrelerini sürekli olarak optimize edin.
6. Pratik Uygulama Örneği
Pratik bir örnek olarak, E-MAX aşındırma ekipmanından sorumlu olduğunuzu ve hazne katodunun erken aşınma yaşadığını ve bunun da D0 (BARC hatası) değerlerinde artışa yol açtığını varsayalım. RF gücünü ve aşındırma oranını SPC sistemi aracılığıyla izleyerek, bu parametrelerin ayarlanan değerlerinden kademeli olarak saptığı bir eğilim fark edersiniz. Bir SPC alarmı tetiklendikten sonra, FDC sisteminden gelen verileri birleştirir ve sorunun haznenin içindeki dengesiz sıcaklık kontrolünden kaynaklandığını belirlersiniz. Daha sonra yeni temizleme yöntemleri ve bakım stratejileri uygularsınız ve sonunda D0 değerini 4,3'ten 2,4'e düşürerek ürün kalitesini iyileştirirsiniz.
7.XINKEHUI'de şunları elde edebilirsiniz.
XINKEHUI'de, ister silikon ister SiC olsun, mükemmel gofreti elde edebilirsiniz. Çeşitli endüstriler için en yüksek kalitede gofretleri sunma konusunda uzmanlaşıyoruz ve hassasiyet ve performansa odaklanıyoruz.
(silikon gofret)
Silikon gofretlerimiz üstün saflık ve homojenlikle üretilerek yarı iletken ihtiyaçlarınız için mükemmel elektriksel özellikler sağlar.
Daha zorlu uygulamalar için SiC yongalarımız olağanüstü termal iletkenlik ve daha yüksek güç verimliliği sunarak güç elektroniği ve yüksek sıcaklık ortamları için idealdir.
(SiC gofret)
XINKEHUI ile en son teknoloji ve güvenilir desteğe sahip olursunuz, en yüksek endüstri standartlarını karşılayan gofretleri garanti eder. Gofret mükemmelliğiniz için bizi seçin!
Gönderi zamanı: 16-Eki-2024